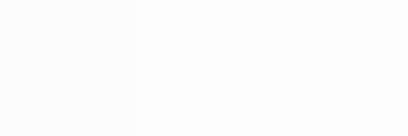
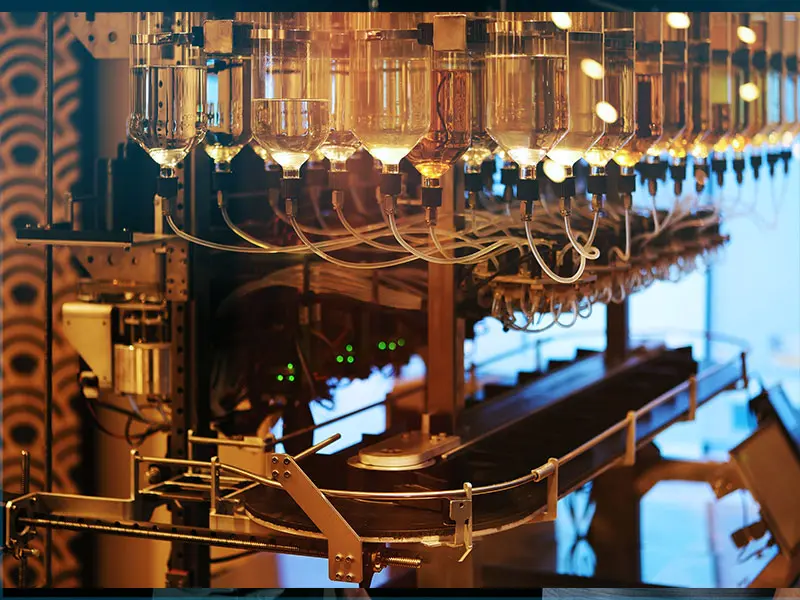
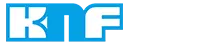
Lifetime Monitoring of Industrial Fluid and Gas Pumps at KNF
Scalable, performant and globally available
Initial Situation and Challenge
Until recently, KNF Group relied on local database-driven tools to record and analyze lifecycle tests of newly developed pumps. However, the system proved too inflexible and lacked the scalability required for modern testing environments. In collaboration with consultants from b.telligent, KNF Group decided to implement a new IoT-based cloud solution using Microsoft Azure. This new solution was designed to flexibly integrate additional test pumps and provide high-performance data querying and analysis—nearly in real time. User experience was also a key priority: a user-friendly web app was to be developed for managing and configuring the measurement devices.
Key challenges of the project included:
- Developing a performance-optimized application to connect up to 10 DAQ (Data Acquisition) devices to a mini-PC
- Real-time analysis of measurement data
- Building digital twins of the entire infrastructure, including the physical location, edge devices, test PCs, DAQ units, and pumps
- Establishing an Azure Cloud Foundation as the technical backbone for the new solution.
Solution
These challenges were addressed using asmart, four-phase approach to develop the lifetime monitoring application:
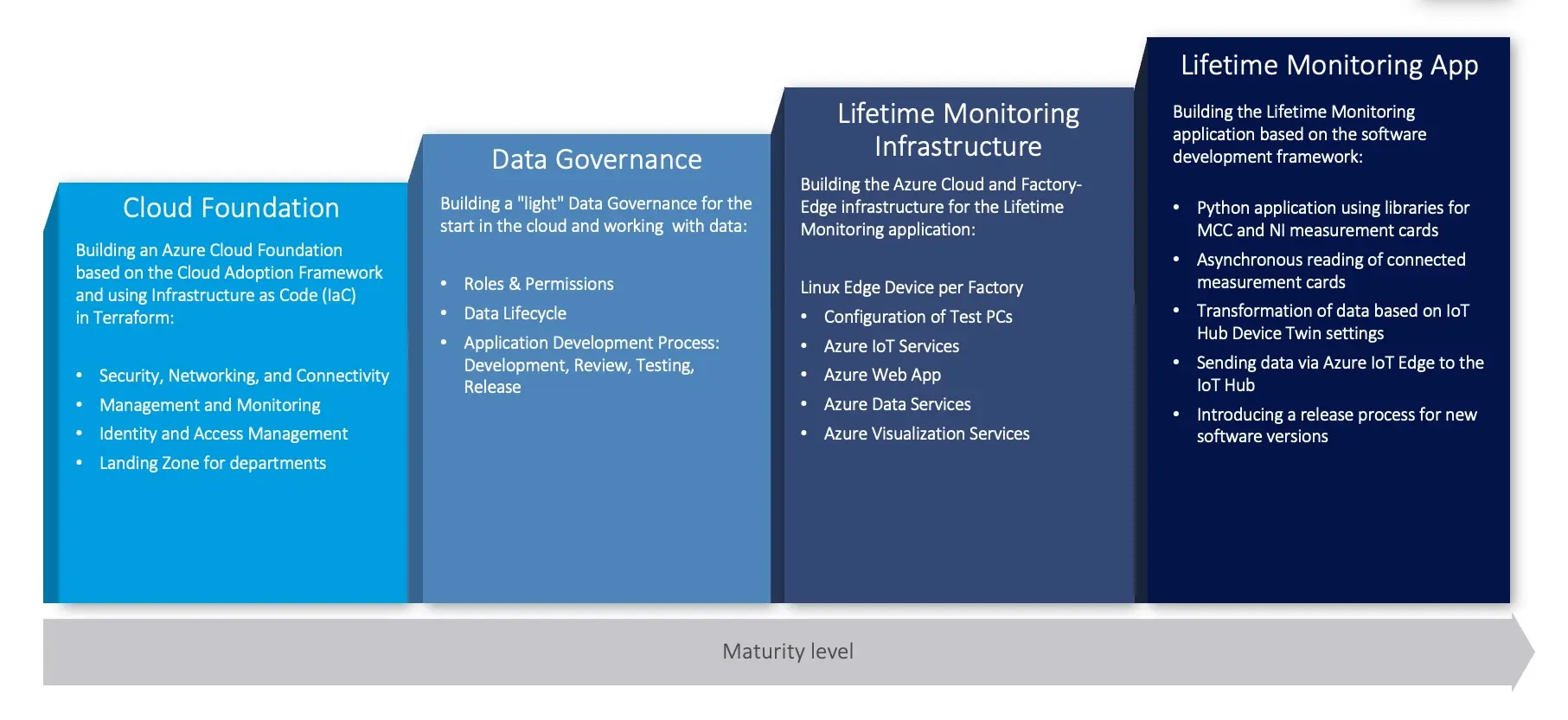
The existing system for collecting and analyzingpump lifecycle test data was securely and efficiently replaced. A tailored andscalable data platform was built using Microsoft Azure IoT services.

The four key components of the application:
- Lifetime Monitoring Software: Enables parallel reading of measurement devices, data transformation, and connectivity to Azure IoT Edge Services and the IoT Hub.
- (Near-)Real-Time Data Processing: Azure Data Explorer enriches incoming data from the IoT Hub with metadata from the Digital Twin Service and makes it available in real time.
- Visualization: Azure Managed Grafana provides dashboards displaying test measurement data with filter options by pump and sensor.
- Test & Device Management: All data models for sensors, devices, and their relationships to test configurations are managed in Azure Digital Twin Service. Test setups are configurable through the web application.

The core of the developed solution is Azure Data Explorer, which stores, processes, and analyzes time-series data. In combination with Grafana, this setup allows test engineers to continuously monitor pump test runs, configure alerts, and flag anomalies. This environment also forms the foundation for future long-term test reports, which will be created using Power BI.
Voices From the Project
b.telligent Services at a Glance
Project Management
Project management for IoT connectivity and traceability solution
Cloud Solution
Design and build a scalable cloud solution
Cloud Engineering
Based on b.telligent's infrastructure-as-code frameworks
Data Processing & Integration
Data processing & integration of external systems using the b.telligent Metafactory
Web Application
Building a traceability portal web application
Data Science & Analytics
Data-based optimization of scrap, production speed and manufacturing capacities
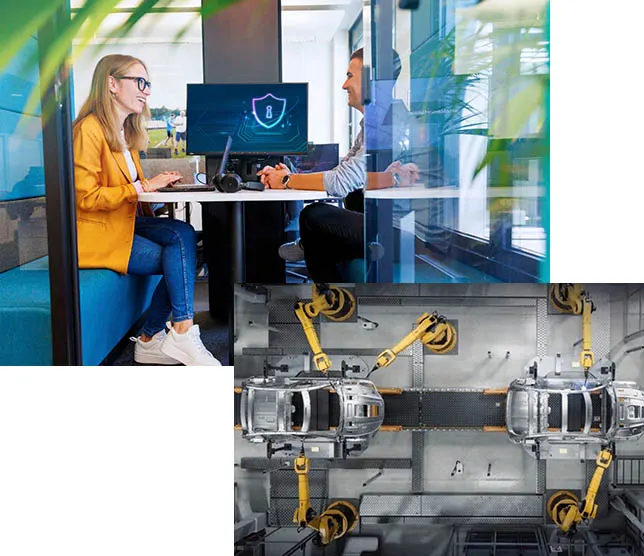
Results & Successes
Robustness and Reliable Release Process: The application was developed with a focus on robustness, featuring a comprehensive testing and release process to ensure stability.
Cloud Foundation as a Strategic Backbone: The Microsoft Azure-based foundation provides a secure and scalable basis for future applications and services, ensuring centralized monitoring and compliance across the platform.
Increased Flexibility and Scalability: The solution enables seamless integration of additional pumps, allowing foreffortless future expansions.
By implementing this modern, Azure-based solution, KNF Group achieved remarkable outcomes and significant advancements. All global sites can now access vital information in (near-)real time, and new test pumps can be integrated easily and flexibly. Another key highlight: thanks to long-term data storage, the system is now future-ready for AI-driven applications.
More Highlights:
Real-Time Analytics Across Global Sites: Data evaluation and visualization are now real-time, enabling worldwide teamsto access key insights instantly.
Long-Term Storage and AI Readiness: With long-term data storage in place,collected data is available for future AI applications, unlocking newinnovation potential.
Improved Usability: The user-friendly web application simplifies test configuration and management,significantly enhancing operational efficiency.
With this modernization, KNF can now work faster, more securely, and more flexibly in the cloud. New topics and use cases can be implemented rapidly. Furthermore, the introduced edge infrastructure offers a solid and robust foundation for continued digitalization of manufacturing.
The Tech Behind the Success
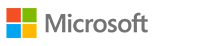
Microsoft
Innovation and integration, as well as interoperability, are key factors of the Microsoft product development. Learn more about our collaboration!
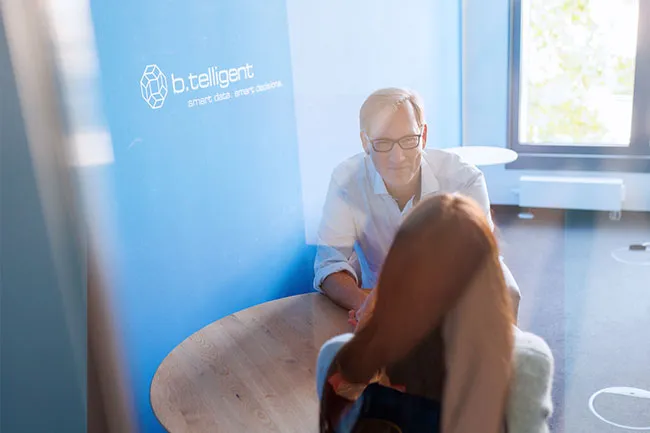
Download the Full Story
Want a handy PDF version of our success story? Whether you need it for yourself or to introduce the project to your team, download it now and explore the full success story. Enjoy reading!
Inspired?
Did our success stories spark your interest? If you're facing similar challenges in data, analytics and AI and look for expert support, let’s talk. A brief call can reveal how we can help you move forward.
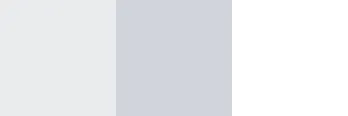