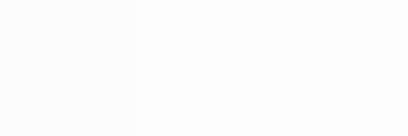
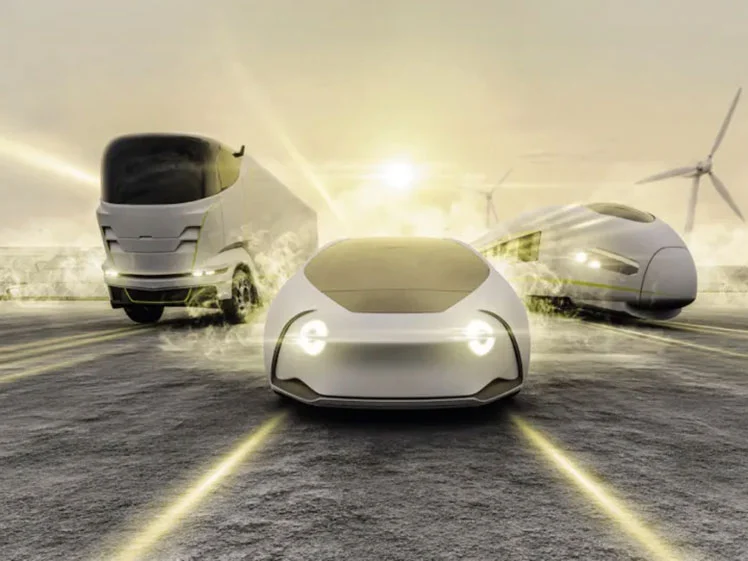
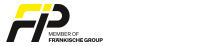
Implementation of a Central Traceability System
Transparency and Quality Secured
Initial Situation & Challenges
Establishment of a central system for tracing the origins of components was of crucial importance to Fränkische Industrial Pipes (FIP). The aim was to record the production process from raw materials to delivery in order to meet increasing requirements for transparency and at the same time proactively ensure product quality. Such a system must continuously link master, process, and quality data to each individual product to create a digital representation of that product.
A key challenge for FIP initially was to further develop existing processes so that they enabled telemetry and quality data to be linked to products. In addition to the internal change process, this required a technologically flexible solution that could also be used to implement other use cases and be made available to internal as well as external stakeholders.
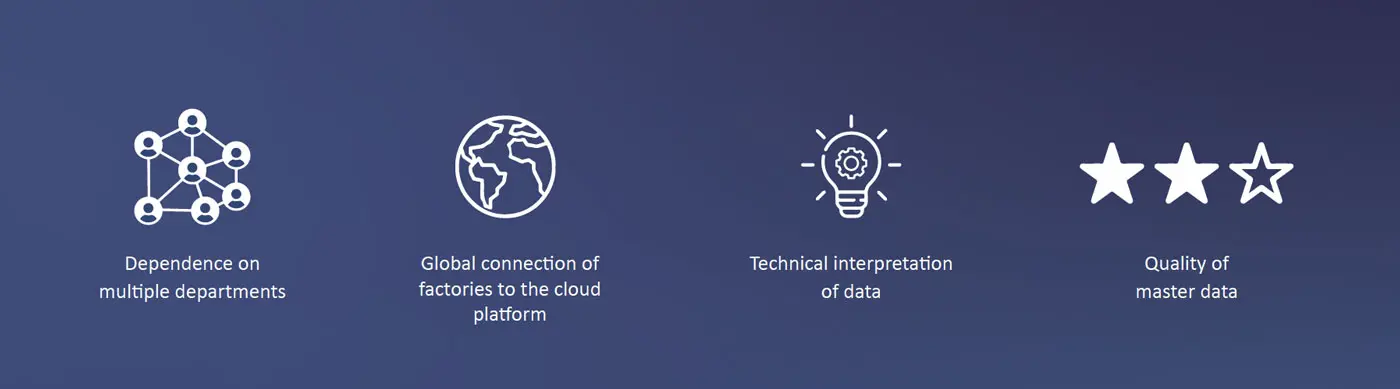
About FRÄNKISCHE Industrial Pipes
FRÄNKISCHE Industrial Pipes (FIP) develops and produces customer-oriented, innovative solutions in the fields of fluid management and protection components, charging and storage applications, as well as battery and thermal management for the automotive sector and industry. As a wholly owned subsidiary of the owner-managed FRÄNKISCHE Group, FIP is a globally active partner to renowned customers with locations in Africa, Asia, Europe, and North America. The company is headquartered in Königsberg, Lower Franconia, Germany. Spun off from FRÄNKISCHE Rohrwerke in 2008, the company employs around 4,400 people worldwide.
Solution
The aim of the portal solution was to ensure effective traceability and digitize conventional production as part of the process chain. To this end, the focus was not only on establishing a robust cloud architecture but also on digitizing the various production processes.
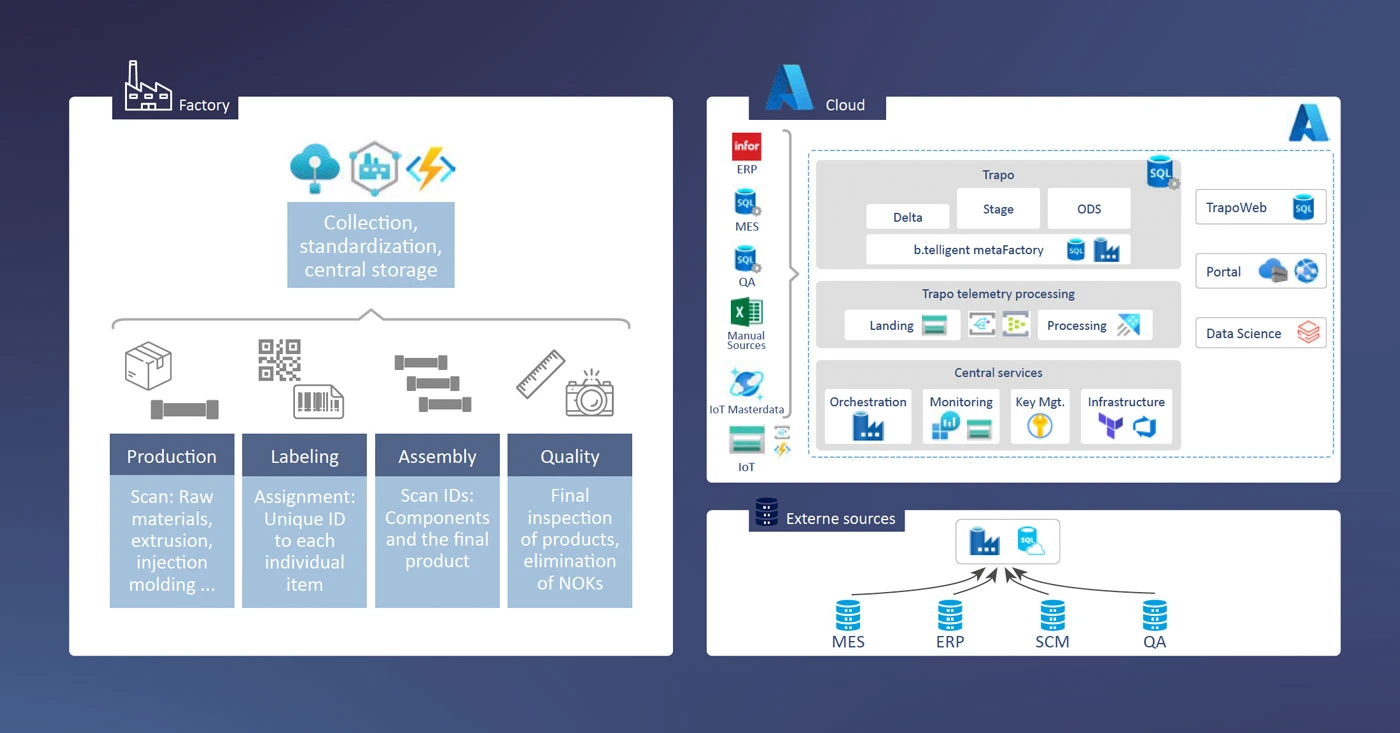
A flexible and highly scalable edge and cloud architecture enabled the smooth integration of data into the various production processes. In the cloud, telemetry data collected from the edge are now linked to ERP, MES, SCM, and quality data and made available in the traceability portal. A central element of the architecture is the Azure Data Explorer, which allows time-series data generated at globally distributed factories to be processed in near real-time and represented in the portal. In addition, it was important for the architecture to be flexible enough to process and store different data types.
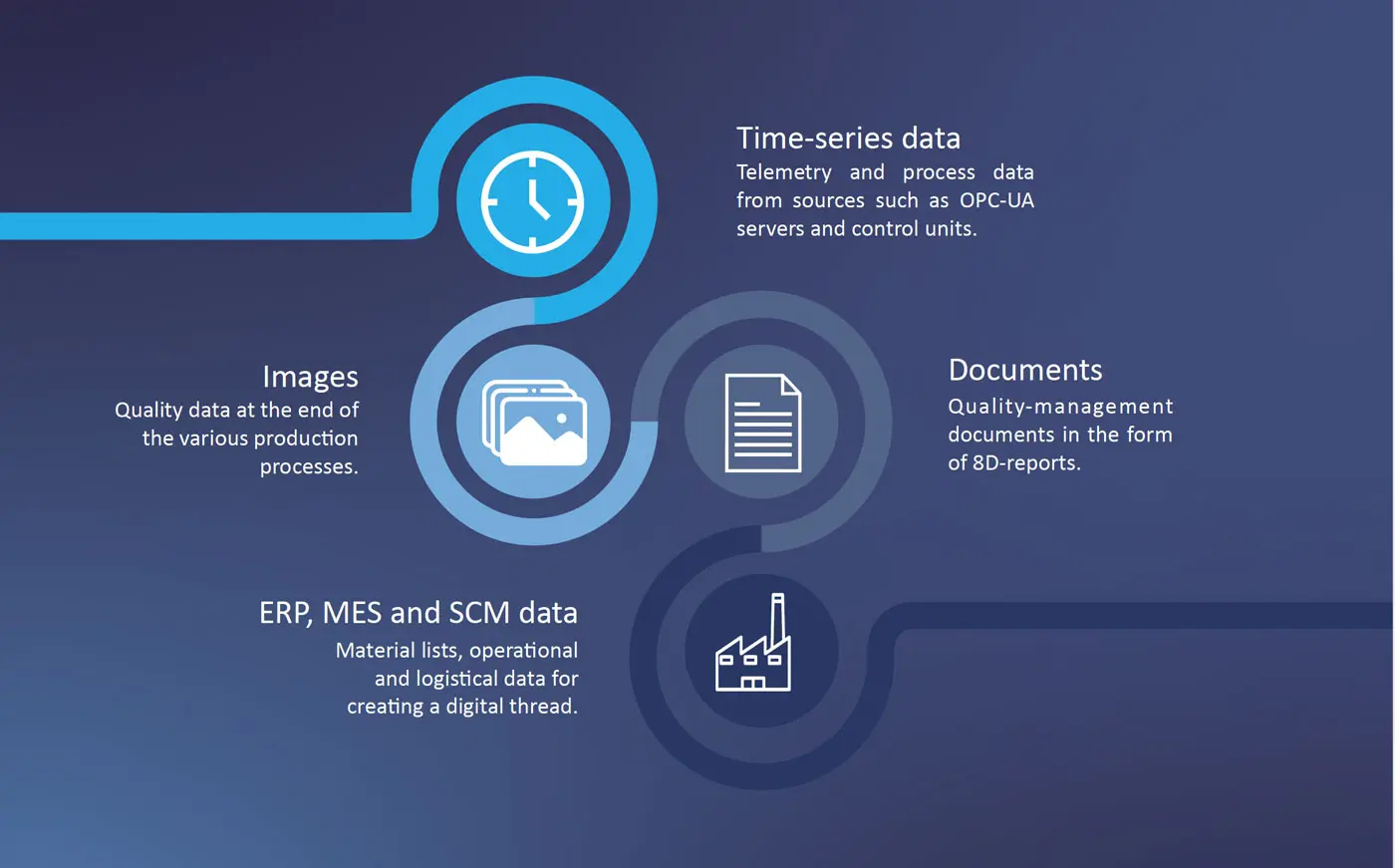
The database generated in this way forms the basis for the presentation of different areas and for searches in the portal solution.
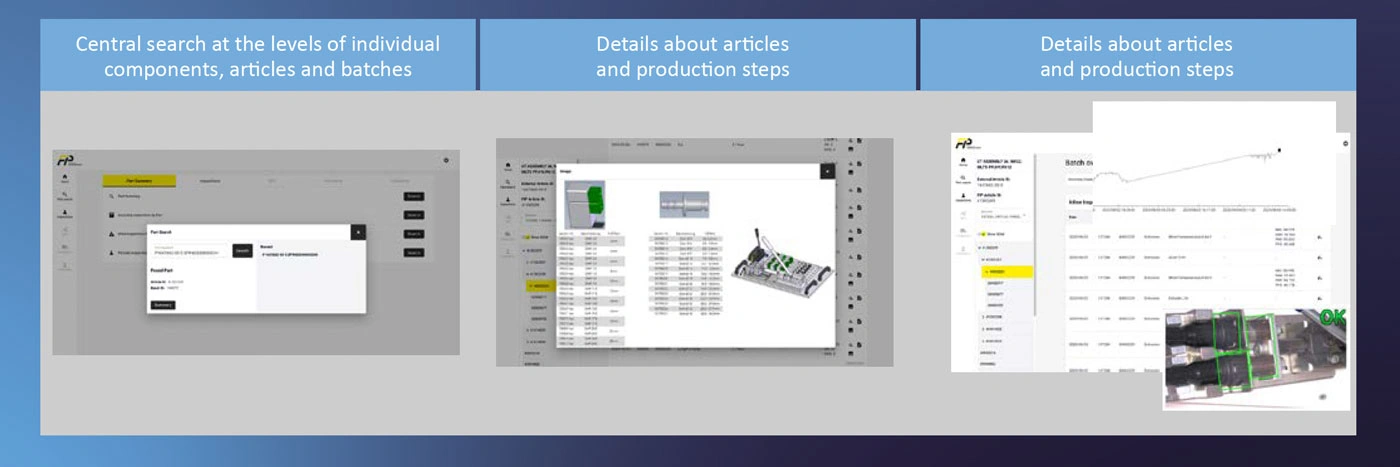
Voices From the Project
b.telligent Services at a Glance
Project Management
Project management for IoT connectivity and traceability solution
Cloud Solution
Design and setup of a scalable cloud solution
Cloud Engineering
Based on b.telligent's infrastructure-as-code framework
Data Processing & Integration
Data processing and integration of external systems with the help of b.telligent's Metafactory
Web Application
Development of a web application forming part of the traceability portal
Data Science & Analytics
Data-based optimization of scrap, production speed and manufacturing capacities.
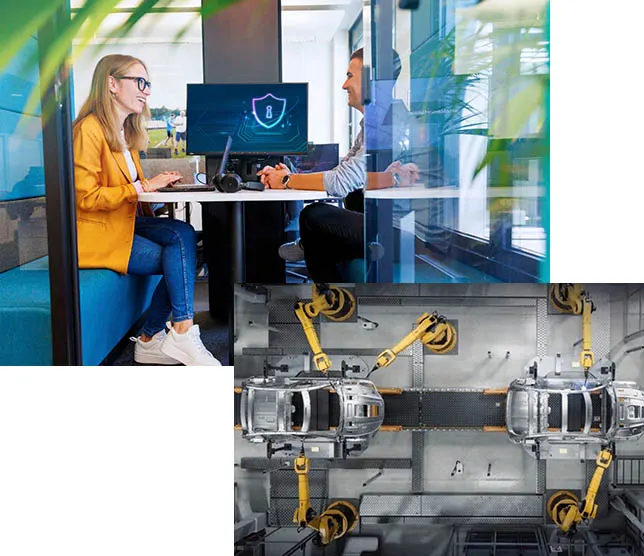
Results & Successes
Quality: Increasing the granularity of quality controls and their automation. Combination of 8D reports and sensor data.
Process Optimization: Data-based, automated evaluation for minimizing rejects as well as optimizing production capacities and speed.
Customer Satisfaction & Regulations: Fulfillment of contractual requirements. Interlinking of supply chains. Planning of subsequent production process. Supply-chain directive, grade A, process optimization guidelines, EU Data Act.
The successful completion of the project allowed us to ensure comprehensive coverage of the manufacturing processes. We successfully integrated all collected sensor and image data, including data from traditional sources such as ERP, MES, and SCM. As a result, the customers of Fränkische Industrial Pipes can now use a productive portal that enables them to operate efficiently and save time.
The Tech Behind the Success
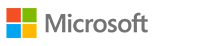
Microsoft
Innovation and integration, as well as interoperability, are key factors of the Microsoft product development. Learn more about our collaboration!
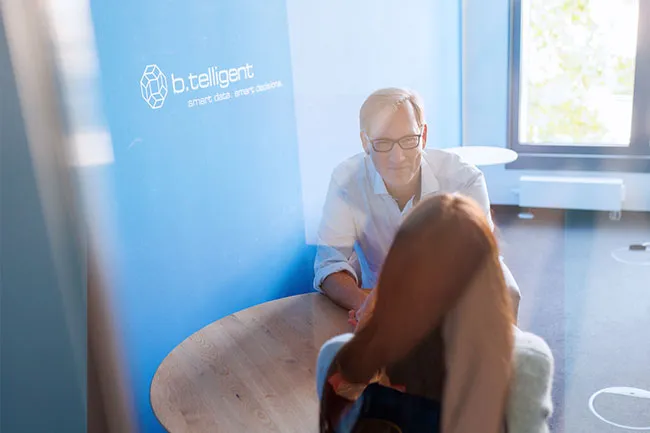
Download the Full Story
Want a handy PDF version of our success story? Whether you need it for yourself or to introduce the project to your team, download it now and explore the full success story. Enjoy reading!
Inspired?
Did our success stories spark your interest? If you're facing similar challenges in data, analytics and AI and look for expert support, let’s talk. A brief call can reveal how we can help you move forward.
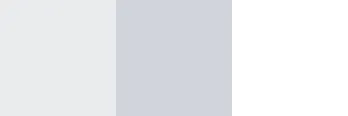